Democratizing Metal 3D Printing: From Napkin Sketch to Metal Part

Description
Plastic 3D printing has become widely accessible across education and industrial institutions, due to significant investment in reducing the technology’s processing complexity and costs. In stark contrast, the adoption of metal 3D printing has been limited to aerospace, medical, and automotive applications due to high cost, technical expertise requirements, operational safety concerns, and the need for expensive ancillary equipment. For example, unlike its plastic counterpart, metal 3D printing typically imposes a strong metallurgical bond between the printed part and the build plate, which requires a large cutting tool to separate the part from the build plate without causing any damage.
Through fundamental research conducted at the VT DREAMS Lab, innovative processing techniques have been developed that reduce the complexity and variability inherent in metal 3D printing. One of the key advantages offered by these novel processing techniques is the ability to easily remove parts, mirroring the convenience enjoyed with plastic parts. The need for secondary equipment is removed, thus reducing the overall cost of the metal 3D printing process. This project also explores simplified software solutions to materialize conceptual ideas into actual parts. VT DREAMS Lab has developed in-house software that converts 2D drawings into precise printing toolpaths to fabricate these designs in 3D. This approach fosters broader accessibility by (1) removing the need for complex CAD modeling software with a steep learning curve and (2) enabling rapid facile removal of the part from the build plate without the need for secondary equipment. This allows any individual and any industry to transform a simple 2D sketch into a metal 3D part, thus paving way for the democratization of metal 3D printing. Through this project, our team will engage student designers (ranging from K-12 grades to senior-level students in engineering and industrial design) to apply this processing innovation in order to gain understanding of its potential impact on design realization.
Documentation
Additive Manufacturing (AM) has fundamentally changed manufacturing and product design. Its layer-wise fabrication approach has enabled the realization of artifacts with significant geometric complexity. Its digital workflow has altered global access to manufacturing. The democratization of AM, in the form of desktop-scale plastic 3D printing (~2012), transformed design prototyping and "making" for engineers, designers, architects, artists, hobbyists, and students by enabling quick, facile access to a method for creating objects. This has, in turn, disrupted numerous markets thanks to the introduction of new creators who are no longer hindered by a lack of access to making.
While the ability to 3D print metal parts has recently emerged and matured as a manufacturing tool for heavy industry, it has not experienced similar democratization as plastic AM, which precludes access and use by non-experts. This is due not only to the cost and infrastructure needed to operate the metal AM machine and allof its ancillary equipment, but also because of the significant expertise required to run the systems to generate quality parts. The diverse and expert skills required for producing a component via metal AM typically involve a collaborative team of multiple people spanning advanced CAD, toolpath programming, process parameter optimization, technician operation and troubleshooting, and metallurgical expertise, as shown in the top of Figure 1.
The overall goal of this project was to democratize metal 3D printing by creating a workflow that autonomously incorporates all the expert design and processing skills required to successfully operate the system and create a part (bottom of Figure 1). Specifically, we developed a metal AM process workflow (“Sketch to Part”) that enables users (1) to create metal parts directly from a 2D sketch and (2) virtually interact with their designs through an immersive experience in which their sketch is projected onto the build surface prior to printing. This projection allows for real time visualization and alignment of the design in a physical space, which enhances user control and streamlines the transition from virtual design to a physical printed part.
Figure 2 provides an overview of the Sketch-to-Part workflow. The developed workflow is generalizable to any of the metal AM processes. For this project, the workflow was validated on Wire Arc Direction Energy Deposition (DED-Arc), wherein a gas metal arc welder (GMAW) is used to selectively deposit metal.
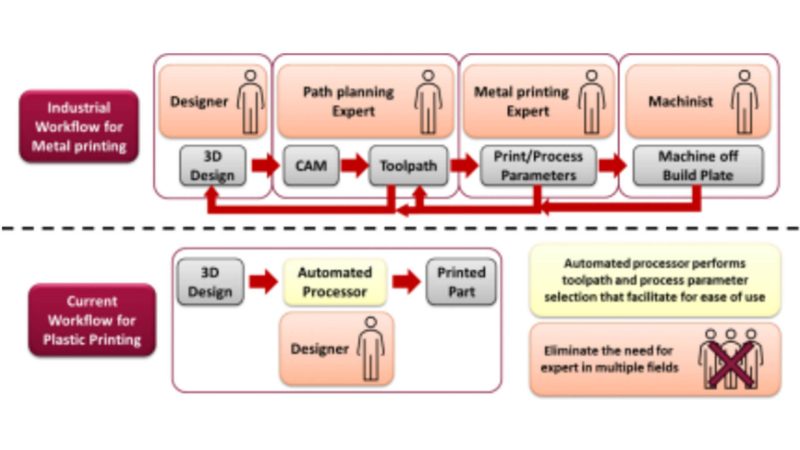
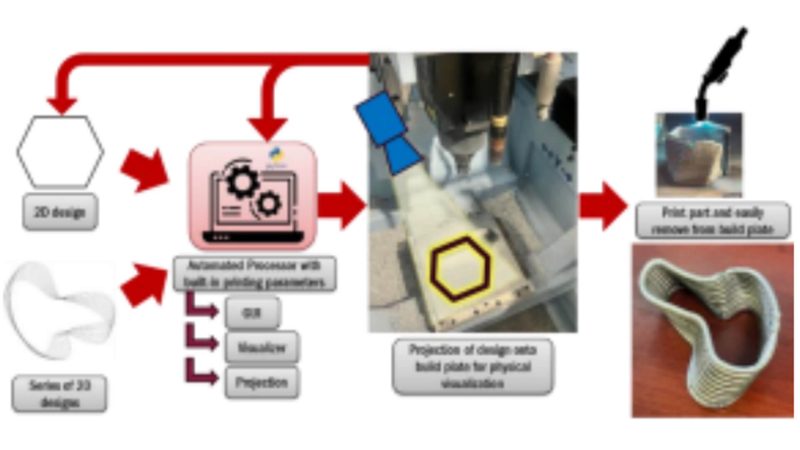
Reports
Our team has run one semester of an IDPro project “Innovative Shaping of 3D Printing Conductive Wires with DED-Arc,” (Fall 2024) mentored by graduate student Bemnet Molla and including undergraduate students Kyle Ray (Mechanical Engineering), Mya Hill (Computer Engineering), and Sai Davanaboyina (Computer Engineering). Each student has been trained in the DREAMS lab and worked toward the goal of Using Wire Arc Additive Manufacturing (DED-Arc) technology to print conductive traces. This goal gave students hands on experience within a research lab focused on rapid prototyping (i.e. Print large and fast). The benefits of the research were to explore the following capabilities:
Generate free form geometries (ie. Innovative shaping)
Control over conductive traces size and shape
Due to large thicknesses, conductive traces provide structural reinforcement
The work and outcomes of the IDPro team are detailed in their end-of-semester poster. Next semester they will collaborate with other parts of the DREAMS lab to print conductive traces within other materials (ie. Drone manufacturing) and to incorporate arts-based research into the project. The IDPro team will continue to Spring 2025 with the original mentor and undergraduates continuing and 3 new students joining: Arushi Chintakayala (General Engineering), Damon Brewer (Creative Technologies), and Nathan Gaysynsky (General Engineering). Including first-year students and an arts-based student will enable the team to focus more on creative uses of the 3D printer. We also participated in outreach to elementary schools and at the VT Science Festival, and began plans for students to present at Hokie for a Day events in Spring.