Digital Fabrication
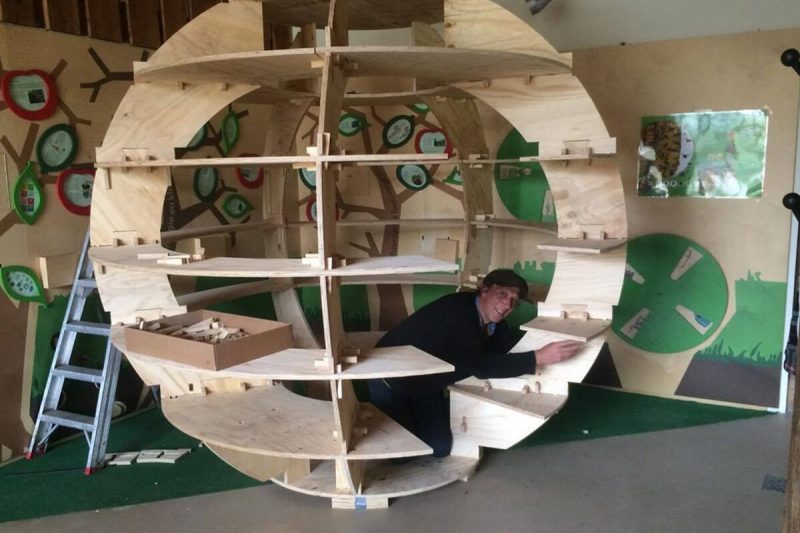
The purpose of this project was to explore digital manufacturing using a low-cost CNC device to augment teaching in the Sustainable Residential Structures (SRS) option of the Sustainable Biomaterials degree. Students graduating from the SRS option work in the construction field and serve as project managers and material experts. Digital manufacturing can incorporate a measure of design thinking into the curriculum and allow the rapid prototyping of new ideas, and the visualization (as well as tactile feel) of how various structures are assembled.
Background
The Maslow CNC (www.maslowcnc.com) is a relatively inexpensive (~$500) CNC machine for cutting sheet goods such as plywood. The Maslow CNC was meant to provide a CNC machine which could be purchased by most anyone and stored in a relatively small space. Unlike conventional CNC machines which lay the product to be cut horizontally, the Maslow CNC is tipped approximately 15 degrees from the vertical (Figure 1). The mechanism of the Maslow is rather unique, using a set of two calibrated motors to move segments of roller chain connected to the sled, which holds a router. A third motor mounted on the depth control of the router can vary the depth of the bit in the material. The router performs the cutting operations and is connected to a wooden sled that can rotate about the center axis to prevent the chains from binding.
The Maslow is controlled by an Arduino circuit board programmed with Maslow’s software (available free). The Arduino plugs into a computer via a USB cable. Maslow’s controlling software called Ground Control is used to calibrate the machine, perform movements of the sled and import g-code files for cutting. The standard g-code format for most CNC files (from such sources as PartKam, Fusion360 and OnShape) are all compatible with the Maslow and were able to produce parts.
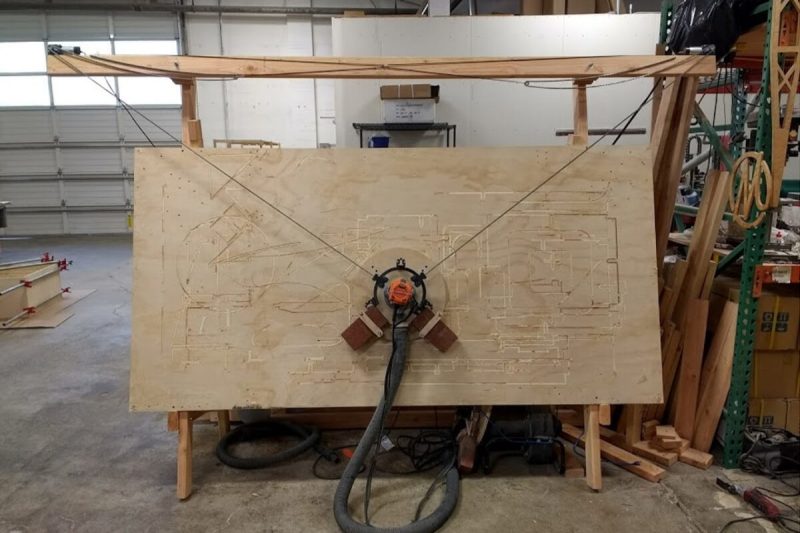
In terms of safety, it should be highlighted that the Maslow is a VERY safe device with the router bit completely encapsulated within the shroud and sled. Students with little experience using a router or woodworking equipment felt very safe around this device. Safety procedures were discussed with the students in case anything happened. Students could simply switch off the main power to the router and controller from a distance if needed. Another safety concern with a router in this situation is fire. The Maslow CNC was continuously monitored during use and while some darkening of material at some places was observed, no fires were observed.
Hindman purchased a Maslow in the Fall of 2016 and assembled it in January 2017. The motivation for purchasing the Maslow was to understand the fundamentals of digital manufacturing and gain experience using tools to create digital objects. Because of the ease of cutting wood and plywood parts, there have been many projects using digitally created objects in parametric designs. Hindman was interested in exploring this topic as a future subject for teaching and research.
Before the ICAT project was initiated, Hindman had worked with several students to build and calibrate the Maslow. Students worked on understanding how the device worked, them how to compile g-code and finally how to use CAD or other software to create objects for construction. At this time, the Maslow was functional but still seemed to have some difficulties with accuracy and control.
Research Methods
The purpose of this project was to explore digital manufacturing using a low-cost CNC device to augment teaching in the Sustainable Residential Structures (SRS) option of the Sustainable Biomaterials degree. Becker from Architecture was invited to participate due to his previous experiences with digital manufacturing. Hindman worked with a student (Mary Geissinger) who helped to use the Maslow and construct several different projects which illustrate different concepts explored. Three projects are highlighted here.
1. Combining Digital Manufacturing and Structural Testing
One of the most common and exciting examples of digital fabrications of buildings is the Wikihouse (www.wikihouse.cc). The project focuses on construction of a house using integrated mechanical attachments (IMA) where the plywood sections are slotted into each other. The building system uses a series of overlapping connections so that once a connection is assembled, the next connection acts to lock the previous pieces together. At the final connection, mechanical fasteners (nails, screws) are used to secure the structure. The method of construction de-emphasizes the use of connections in favor of extra materials. The goal of the project was to create a house that could be constructed with minimal tools and knowledge.
One of the sub-assemblies of the Wikihouse, called Wren (Figure 2), is a mock-up of the main beam systems used in the Wikihouse floor. Wren is made up of several center pieces (not shown in Figure 2), top and bottom sections connected by a dovetail joint, and side pieces connected by a finger joint. The top/bottom pieces are placed on first, then the side pieces overlap to lock in the top/bottom sections. In the full structure, a continuous sheet of plywood is laid across the entire beam to hold the side pieces together.
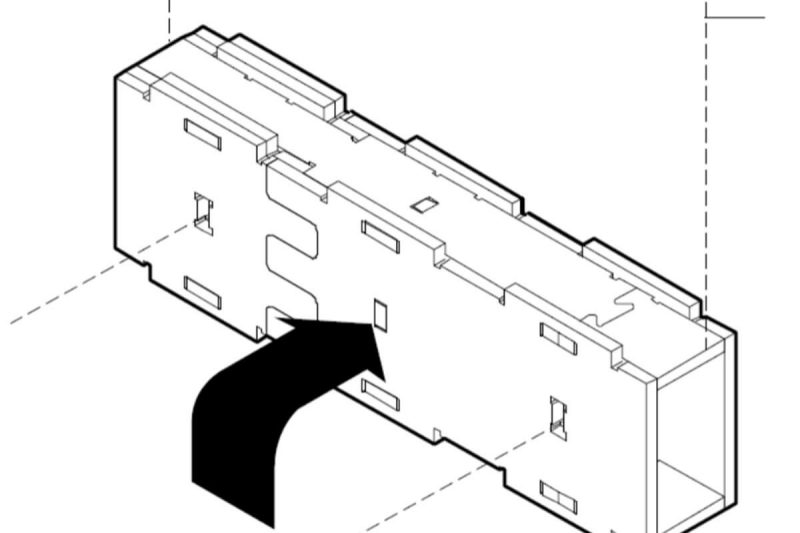
While there has been some interest in digital manufacturing and the use of IMA connections, it is important to point out that these connections and sub-assemblies are not typical of the materials and connections used in most conventional wood construction in the United States. A review of research literature reveals little testing of the use of IMA connections and digital manufacturing structures. To really forward digital manufacturing and make this practical for engineers and designers, structural testing of the digital manufacturing products is needed.
First, to understand the connections and assembly of the Wren, Hindman and Geissinger downloaded the CAD files from the Wikihouse site (Creative Commons license) and created a version of Wren (Figure 3). In order to test the Wren assembly as a beam, a longer length is needed to perform as a structural member. Hindman and Geissinger created a series of continuous side and top/bottom elements which incorporated the finger joints and dovetail joints into both ends of the assembly (Figure 4). These elements could then be connected in a continuous manner to produce a longer beam. This required modification of the original CAD files, then development of the g-code for use in the Maslow.
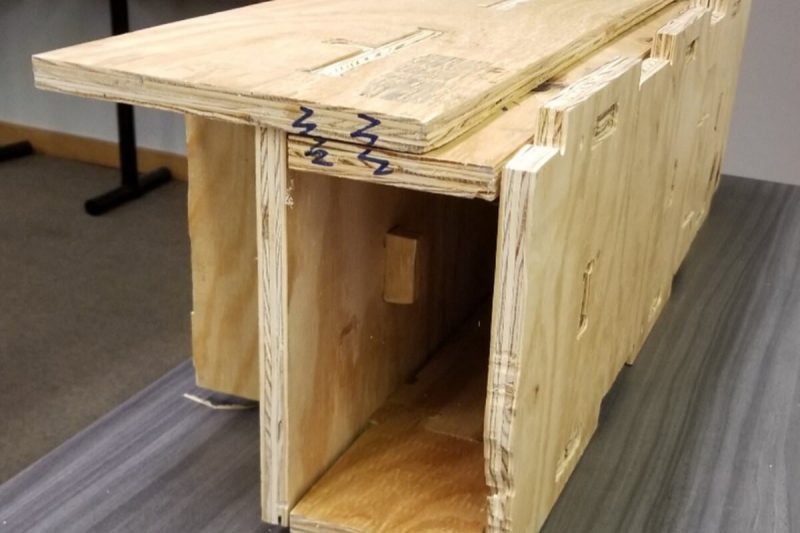
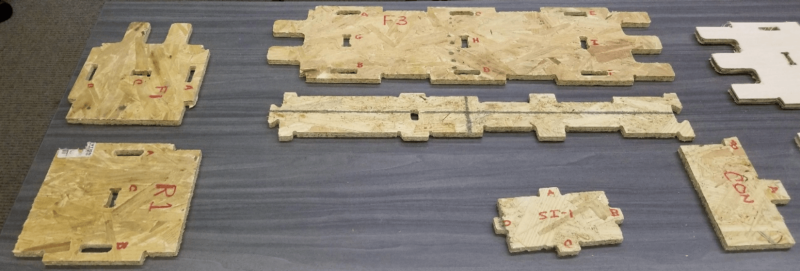
The completed Wren assembly is shown in Figure 5 in the test machine. The beam was loaded by a constant displacement force applied at the center of the beam. The beam held approximately 350 lbs before failure, which was caused by one of the finger joints opening (Figure 6) and separating. This is an interesting failure and points out one of the disadvantages of the IMA connections. This performance is something that Hindman can use as a topic for further research and study.
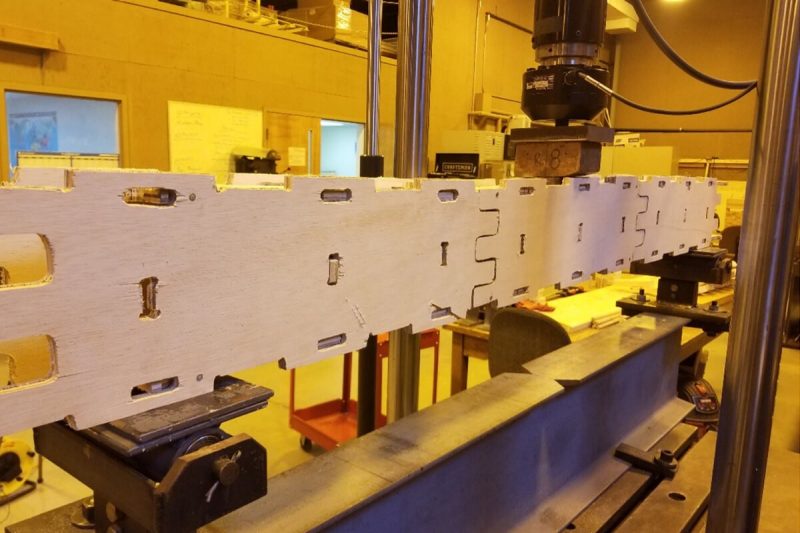
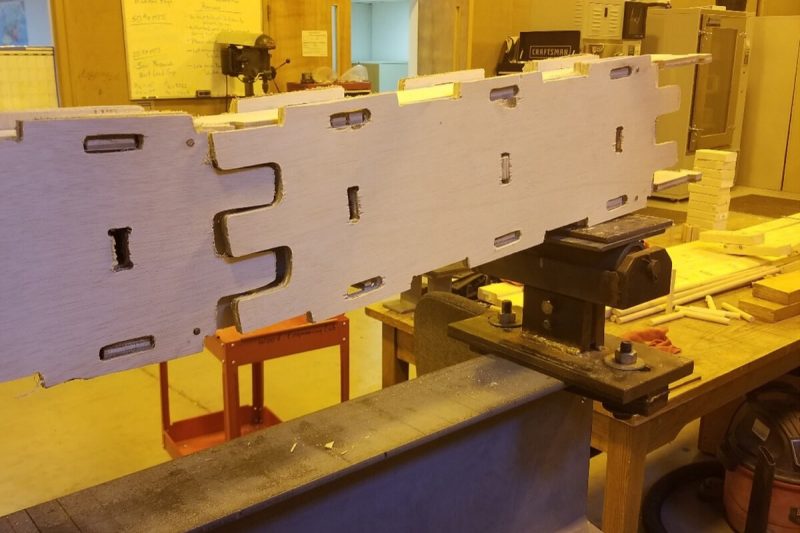
2. Producing Accurate Artwork – Lettering for SBIO Shack
To assess the functionality of the Maslow CNC for accuracy, Geissinger began a project to create lettering that was used to decorate the Society of Renewable Resources (SRR) Shack-a-Thon entry. To accomplish this, Geissinger found a set of letter templates, imported them into an image program, then produced g-code for each individual letter. The sign is shown in Figure 7 and contains three different cutting practices – Society was made by removing the material, Renewable was a partial cut into the panel, and Resources were letters cut from another panel and attached creating a raised effect. The different cuttings were created using the same CAD files and different g-code commands of cutting to the inside or outside of the shape.
Overall, the improvements to the Maslow funded by the SEAD Mini grant made the tool much more accurate and useful. This project was a nice demonstration of that accuracy.
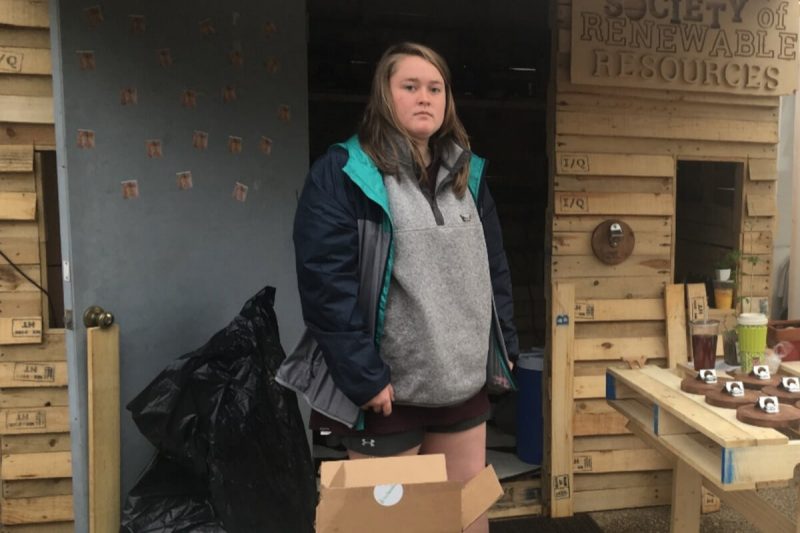
3. Producing a Functional Structure
While the two previous projects demonstrated that structural sections and lettering with high levels of detail could be created using the Maslow CNC, the final project combined these elements into a visible project that can be used for demonstration of the Maslow capacities and also as a teaching tool. IKEA has released a Creative Commons project called the Growroom (Figure 8) which is a large sphere constructed of CNC cut plywood. The original version housed a series of plants on each of the shelves.
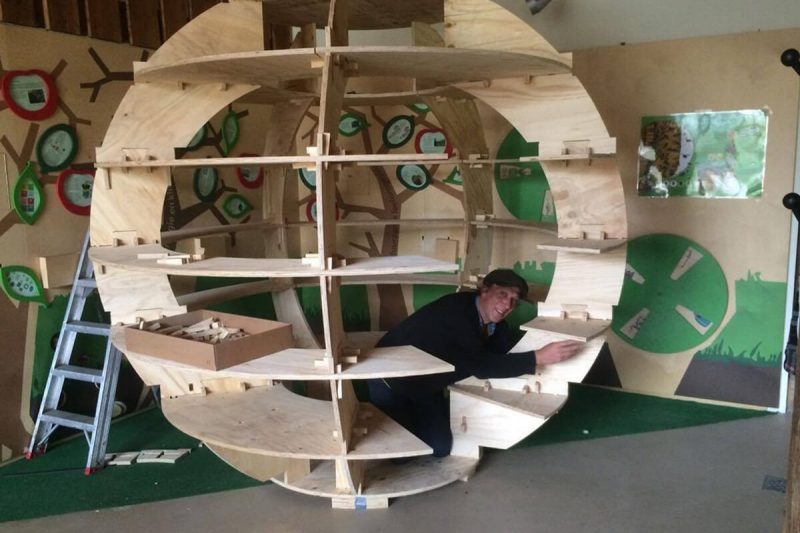
Hindman and Geissinger have begun the production of the parts needed for the Growroom. Unfortunately, the timing did not allow for the completion of the Growroom by the ending of the SEAD Mini Grant. Geissinger was able to translate the parts into CAD software, and both Hindman and Geissinger worked to create the g-code needed to create the parts on the Maslow. Hindman is currently continuing to work on cutting out pieces for the Growroom and anticipates that the sections will be done by September. The Growroom uses a combination of IMA joints, dovetail joints and small wedges to lock the pieces together. The entire project is estimated to use twelve sheets of plywood. After all the parts are made and sanded, they will be finished with a polyurethane coating to protect the parts. The hope is to introduce students to digital manufacturing by showing them the Growroom parts, talking about how it was designed and made, then having classes actually assemble and disassemble the structure.
Next Steps
The next steps for this project are to finish producing parts for the Growroom over the summer. Approximately 1/3 of the parts are produced at this time. The PIs would like to use the completed Growroom as well as other projects for an ICAT Playdate at a future time. Hindman is planning on offering a special study class in Digital Manufacturing of Buildings in Spring 2020. This class will expose students to the Maslow and have them operate it for a variety of projects.
For Hindman, this project was a new experience which has allowed exploration of a new area of work and teaching. Digital manufacturing is still being understood as a tool and method for use in construction. Future use is highly probable given the accuracy of production and need for greater precision on the jobsite. The area itself is still struggling to mature and find ground in the area of research.
ICAT 2018-2019 Mini Sead Grant